Harness the power of continuous manufacturing with advanced excipients
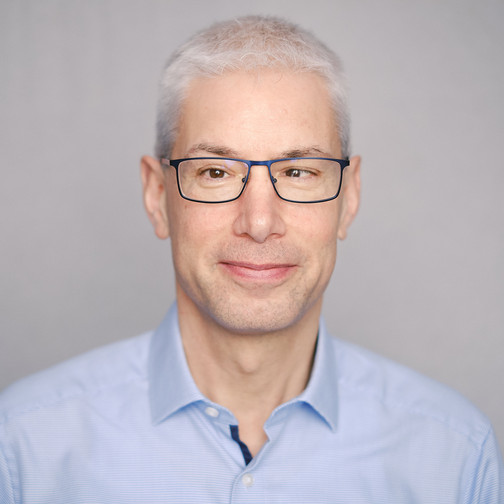
By Meinolf Brackhagen
Senior Research Scientist, IFF Pharma Solutions
Over the past decade, the use of continuous manufacturing has increased within the pharmaceutical industry. Today, drug developers are increasingly focused on refining and optimizing these processes. Unlike traditional batch methods, continuous manufacturing integrates production steps into a seamless, ongoing production line—reducing manufacturing times from months to days.i
Establishing a continuous process for developing solid oral dosage forms requires strategic excipient selection. Read on to explore the critical and unique roles different excipients play in continuous manufacturing—and how the right excipient can enhance drug product quality, tablet integrity, and production efficiency. But first, why choose a continuous manufacturing process?
The benefits of continuous manufacturing
Continuous manufacturing uses real-time monitoring and advanced quality control techniques, such as Process Analytical Technology (PAT) and Quality by Design (QbD), which are integrated throughout the manufacturing process (see figure 1). This allows for immediate adjustments and better control over process parameters—minimizing the risk of human error and variability.ii As a result, continuous manufacturing leads to consistent production of high-quality products, thereby reducing the incidence of defects and recalls.iii
Figure 1. Comparison of a typical batch manufacturing process to a conceptual integrated continuous manufacturing process.1
In addition, the uninterrupted flow of continuous manufacturing enhances efficiency by reducing production times. In fact, companies that have adopted this process have reported significant reductions in manufacturing and testing cycle times, sometimes by as much as 80%.3 This cycle time improvement is particularly beneficial when responding to high demand or emergency situations where rapid production is crucial. What’s more, continuous manufacturing can significantly increase production yields by eliminating the downtime associated with batch processing, leading to long-term financial benefits. The ability of these systems to integrate various production stages into a single, streamlined process also reduces the need for extensive storage and transportation of intermediate products, which further minimizes costs while reducing the environmental footprint of manufacturing.2
The flexibility and scalability of continuous manufacturing systems means that production can be ramped up or down easily to meet market needs without the extensive reconfiguration required in batch manufacturing. This ensures a more responsive and resilient supply chain.3 Advantages of continuous production are many; however, it is not without challenges. Startup costs are high due to retiring old batch equipment, purchasing new continuous manufacturing systems, and training staff and technicians. What’s more, a deep understanding of excipients is necessary to determine which are best suited to optimize the process.
The multi-functional roles excipients play in continuous manufacturing
Excipients, the inactive ingredients in drug formulations, play a critical role in the success of continuous manufacturing, and, therefore, the quality and performance of final drug products developed through this method. Here’s how:
1. Ensure a steady feed flow for consistent high quality
Steady feed flow is essential during continuous manufacturing in order to prevent process interruptions and ensure consistent quality and production efficiency. Excipients with predictable material properties, like particle morphology, density and size, are crucial for maintaining a steady feed into the continuous manufacturing system. Variability in these properties can lead to fluctuations in this process, potentially compromising product quality.iv Take hydroxypropyl methylcellulose (HPMC) as an example. Its particle morphology can significantly influence powder flow, which affects segregation in the hopper/feeder and uniformity of the formulation. The flat particle shape of HPMC polymers can cause the particles to form a bridge over the hopper outlet which restricts material flow and ultimately causes large variation in directly compressed tablets.
To overcome this challenge, the team at IFF Pharma Solutions has found that switching to an excipient with a more rounded particle morphology, such as METHOCEL™ DC2 HPMC, can improve the material flow in a hopper. This has been shown to reduce the variability in tablet weight (range of 7.0 to 7.8 mg) when compared to standard METHOCEL™ CR HPMC (range of 6.2 to 7.8 mg), leading to a four-fold decrease in tablet rejection rates (0.11% vs. 0.51%).v
2. Enhance tablet strength with the right binder
The choice of excipients used in a formulation manufactured through a continuous system can also influence the performance attributes of the drug product, such as its dissolution rate, stability and bioavailability. By selecting excipients that enhance these properties, manufacturers can produce drug products that provide better therapeutic outcomes for patients.4 For instance, binders are crucial for ensuring the structural integrity of tablets formed during continuous manufacturing. The choice of excipient binder and its concentration can affect the hardness, disintegration time and dissolution rate of the final product.
Microcrystalline cellulose (MCC) excipients are often used for their superior binder properties. However, in direct compression continuous manufacturing systems, there is a need for superior mixing, flow and compressibility of MCC. To solve this challenge, the co-processed excipient, Avicel® SMCC (a synergistic combination of MCC and colloidal silicon dioxide) provides a key advantage leading to the formation of stronger tablets. At IFF Pharma Solutions, our diverse MCC offering means that customers can easily find a suitable grade of MCC, from the leading industry standard grade for direct compression (Avicel® PH102, and Avicel® PH 200) to special grades, like Avicel® DG, which is designed to preserve re-compactibility after dry granulation.
3. Balance lubrication for smoother manufacturing
Lubricants, like magnesium stearate, are used in continuous manufacturing to reduce friction during the compression process, preventing the feed flow from sticking to machinery. However, excessive lubrication can significantly affect the dissolution rate of a final drug product by forming a hydrophobic barrier around the tablet. This can hinder the release of the active pharmaceutical ingredient in the gastrointestinal tract, affecting its bioavailability. The solution? A hydrophilic lubricant with a higher melting temperature can enable greater functionality at high press speeds during continuous manufacturing while avoiding the drawbacks of traditional lubricants. One example is Alubra®sodium stearyl fumarate. It delivers the right amount of lubrication, enabling superior tablet performance. Using this excipient as a lubricant has been shown to improve tensile strength, disintegration time and friability, despite prolonged mixing times.
4. Maximize throughput and process efficiency
Excipients also play a role in optimizing the throughput of continuous manufacturing (i.e. the rate at which drug products are produced). Those that facilitate smooth processing and reduce the likelihood of equipment fouling or downtime will contribute to higher production rates. Proprietary research at IFF Pharma Solutions has investigated the role of excipient particle size grade and vibrational assistance on continuous feeding. Results demonstrated that consistent feeding of Avicel® MCC can be optimized through proper selection of MCC grades (particle size and density) and process settings (flow rate and vibrational assistance).
Increasing the feed rate reduced process variability with standard density Avicel® grades (PH-101, PH-102 and PH-200).vi However, increasing the feed rate had a negative impact on high density MCC grades, such as Avicel® PH-302, leading to rat-holing.vii This refers to flow issues where the powder material forms a narrow flow channel through the hopper while the surrounding materials remain stagnant, leading to interrupted production. By incorporating vibrational assistance at fast-feeding rates (i.e. 25 kg/hour), feeding variability can be reduced by half.7 Want to know more? We’ve got a video on this topic – watch it here!
Unlock the full potential of continuous manufacturing
The importance of excipients in the continuous manufacturing process cannot be overstated. They are integral to the production of robust and effective drug products. As the industry continues to embrace continuous manufacturing, the collaboration between excipient manufacturers and pharmaceutical companies will be key to realizing the full potential of this process.
Thinking about making the switch or optimizing your continuous manufacturing process? Contact our team to find out which excipients can keep your production lines running fast and efficiently.
Connect with our experts here.